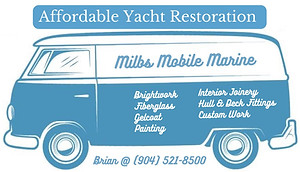
9610 Commonwealth Ave., Jacksonville, FL 32220
Installing Seacock Backing Plates (3-29 & 30-25)
Mar 30, 2025
Over a couple days in the previous week, I fabricated the G-10 backing plates for the new seacocks and generally readied them for installation. It would take a few days of work to install the seacocks, having first to install the backing plates and needing to allow for epoxy cure time. I started Saturday afternoon with further prepping the donut-shaped backing plates by locating the bolt holes by placing the flanged seacocks onto their respective backing plates and marking the holes for the 5/16 bronze machine screws - three per seacock. With the location of bolts marked, I drilled out the holes in the backing plates on my bench top drill press.
I took the through-hull fittings and the backing plates to the boat for test fitting. There was a rather severe angle on the starboard backing plate, and lesser so on the port backing plate. I had previously drilled for the through-hull fittings from the exterior, maintaining a perpendicular (90-degree) orientation with the drill's hole saw and the hull. The 90-degree orientation on the exterior resulted in a less than 90-degree angle on the interior, this was due to the molded fiberglass pan not being co-planer with the hull's turn of the bilge. I taped the through-fittings in place, went inside Biscuit, placed the backing plates over the through-hull fittings and screwed on the backing nuts. I loosened the backing nuts slightly and then rotated the backing plates up until I had the backing plates' surfaces perpendicular to the through-hull fittings. I then verified that the heads of the through-hull fittings were sitting flush on the hull's bottom. To support the backing plates, I moved some wedges in place to temporarily maintain the proper positioning. I decided to reduce the severity of the backing plates' angles by removing material on the bottom of the backing plates' inboard surfaces. I used a flap disk on the angle grinder and tapered the G-10 plates from the centerline and towards their inboard edge. I repeated the test fitting process and continued to work material off the plates until I was satisfied with the fit. The result was a reduction in the severity of the angle of the backing plates - becoming slightly more in plane with the molded pan.
I took the backing plates back into the shop and inserted foam ear plugs into the through bolt plugs - this was to keep thickened epoxy from fouling the holes. The cramped quarters makes this installation a bit tougher, and so the pre-drilled holes will allow me to keep the drill moving in the proper orientation to the backing plates - 90 degrees to them. The foam ear plugs will be removed prior to drilling for the bolts.
I then mixed two pots of epoxy: the first being "neat", that is no thickening agent; the second being epoxy thickened with a combination of 406 colloidal silica and 404 high-density filler. I painted the neat epoxy onto the backside of the backing plates and the surface of the molded pan and then applied the thickened epoxy to the inboard half of the backing plates. With the backing plates prepared with epoxy, I then carefully placed them over the through-hull fittings that were taped in place. The threads of the through-hull fittings were also taped to protect from accidental contact with the epoxy. The wedges were then repositioned and the backing nuts screwed onto the through-fittings to insure proper orientation of the backing plates. I again verified the through-hull fittings were sitting flush on the hull's surface. I waited until the thickened epoxy cured to a point where I could remove the backing nuts and through-hull fittings without disrupting the positioning of the backing plates. My final task for the day was to apply the same thickened epoxy mixture to the inside of the hole and pressing the epoxy filler into the outboard void, essentially sealing the hole from the interior of Biscuit. I applied just enough thickened epoxy to glue the backing plates in their final orientation. When I left the shop there was still a void on the outboard edge of the backing plates, where the wedges were helping to support the orientation of the plates.
The following day, I spent most of my time sanding the filler applied from last week's work - small voids on the overhead of the interior, as well as the work done on the backing plates for the seacocks. With the sanding complete, I turned towards clean up - vacuuming the interior and solvent-washing the areas requiring more epoxy work. I removed the ear plug bungs - worked perfectly - and reinstalled one for both the bolts on the outboard edges. This bolt was sitting over the portion of the backing plate that was raised over the molded pan and required thickened epoxy to be pressed into the void. I mixed the 406/404 thickened epoxy combination and applied it to the voids on both the port and starboard backing plate, and also created a fillet from the vertical surface of the backing plate to the molded pan. Sanding will improve the fillets' appearance prior to painting. The backing plates were in! Sanding and painting are next - prior to installation of the seacocks.
Finally, I applied a fairing coat (410-microlight) to the starboard side of the vertical surface where the head was located - the port side is ready for paint.
Total Hrs: 6.5
